Our expertise
For nearly a century, Panaget has been manufacturing exceptional wood floors from French oak, thanks to the dedication of the people who work for the company. Our employees combine skill and expertise to create the wood floors of tomorrow, embodying the renowned ‘French touch.’ Every day, we commit to providing our customers with high-quality, safe, and sustainable products.
Our French Oak
The wood sourced by our sawmills comes exclusively from French forests and is selected by expert buyers with whom Panaget has long-standing relationships. French oak, globally recognized for its high quality, is one of the hardest and densest among European tree species. Its slow and steady growth in our French forests gives it its golden hue, while its closely spaced growth rings provide unparalleled aesthetics.
Sawmills
We work with about forty French sawmills that source wood from forests located within 500km of our factories. 95% of this wood is PEFC certified, ensuring its origin and our commitment to sustainable forest management. From the beginning, we’ve utilized the entirety of the wood processed by our partner sawmills. This allows us to offer a very extensive and varied range that enhances this noble material.
Receiving wood
Each day, we receive trucks carrying rough-sawn or milled wood as well as components used in wood floor production (plywood/HDF cores and stabilising layers). Our wood buyers inspect each delivery and ensure it meets our strict quality requirements.
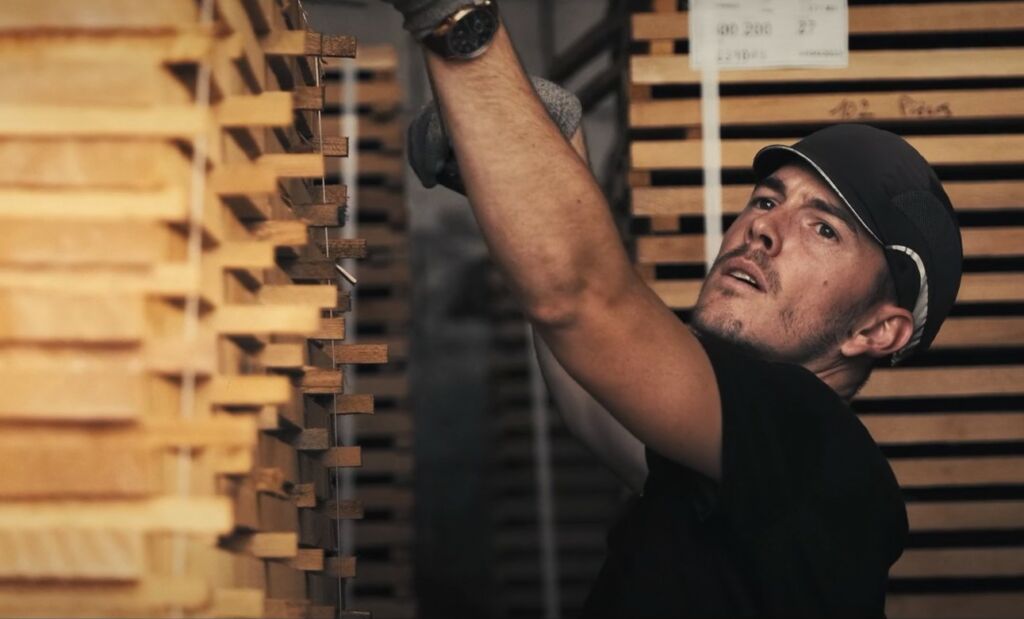
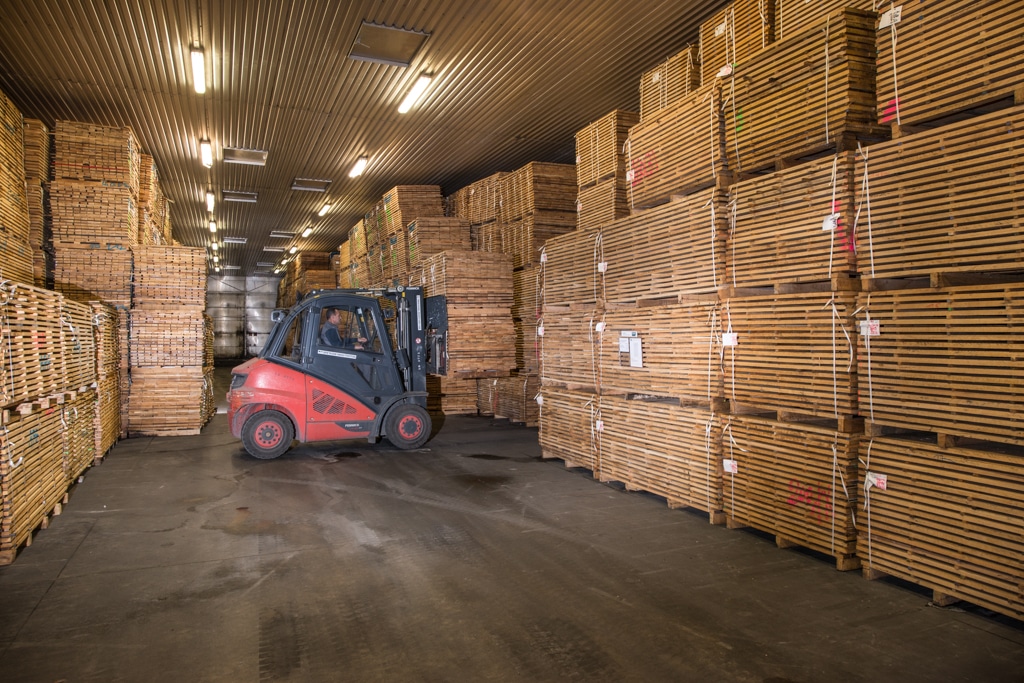
Drying
As a crucial step for quality wood floors, drying is essential to ensure its stability. That’s why Panaget manages this process in-house in two stages:
Pre-drying: The goal is to homogenize the wood’s moisture content upon reception to about 25%. This slow process (60 to 90 days) allows for gentle handling of the material.
Kiln drying: At Panaget, drying is done in traditional 30m³ chambers, allowing for a drying cycle tailored to each batch of wood (species/moisture level). The temperature can reach 67°C, eliminating all wood-boring insects. Panaget prioritizes a natural rather than chemical approach, which is also more effective. At the end of the cycle, the wood’s moisture content is about 7%.
This process has been perfected over nearly a century and ensures the stability of our veneers.
Planing
Planing is the first step in wood processing and is used to calibrate (planing on all four sides and cutting to length) the boards for the next stage of sawing.
Sawing
Here, the veneers are cut to the desired thickness, depending on whether they’re intended for domestic or commercial use. The wood processing generates sawdust and wood chips that power our biomass boiler, contributing to our energy independence (wood drying, building heating, etc.). All other waste is repurposed through specific recycling channels.
Sorting
In 2019, Panaget invested in high-tech scanners to improve veneer sorting, making it more reliable, quicker, and optimizing the use of oak. Our Methodologies team configures the scanner to specific parameters for each wood grade: Classic, Authentic, Zenitude, etc.
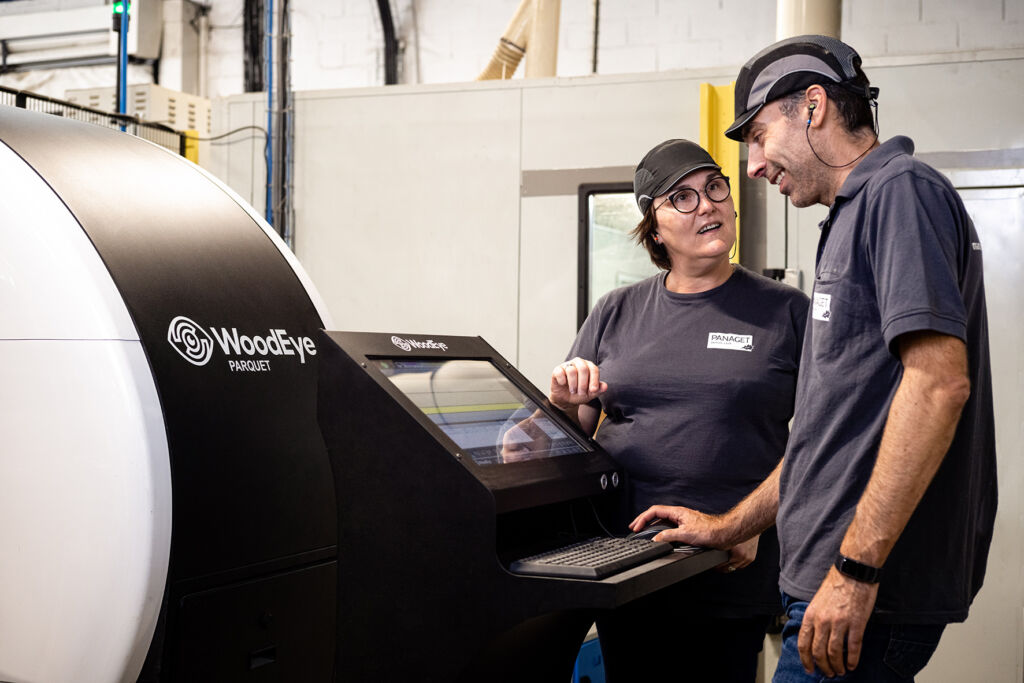
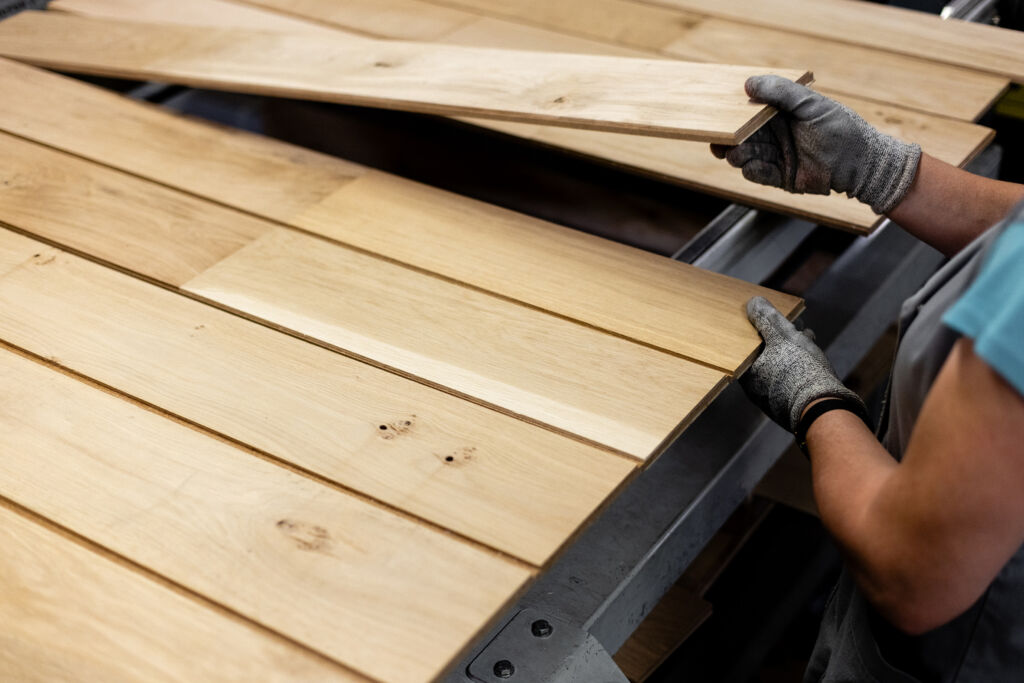
Assembly & Finger Jointing
To maximize our raw materials, we use veneers of different lengths and widths. We glue their edges to create multi-strip wood floors or finger-jointed wood floors, simulating the traditional variable lengths flooring.
Gluing
The noble wood veneer, the core (plywood or HDF), and the stabilising layer are assembled to create engineered wood flooring. Thanks to its structure, this type of wood floor is more stable than a solid wood floor. Panaget uses hot pressing to ensure even glue distribution, providing a durable bond. The adhesives used have been specifically selected and tested to ensure our wood floors achieve an A+ rating for indoor air quality.
Filling
Panaget places a high priority on the aesthetics of its wood floors, focusing on filling imperfections (knots, splits, cracks, etc.). That’s why we use a natural wood cellulose-based filler, which is more eco-friendly than plastic-based fillers. This filler can also be brushed and tinted for a subtle finish. Panaget has invested in automated filling to ensure optimimal reliability.
Machining
Maching is one of the final stages in the manufacturing process and creates the assembly system: click-lock or tongue-and-groove. This determines whether the wood floor is installed with a click system or to glue.
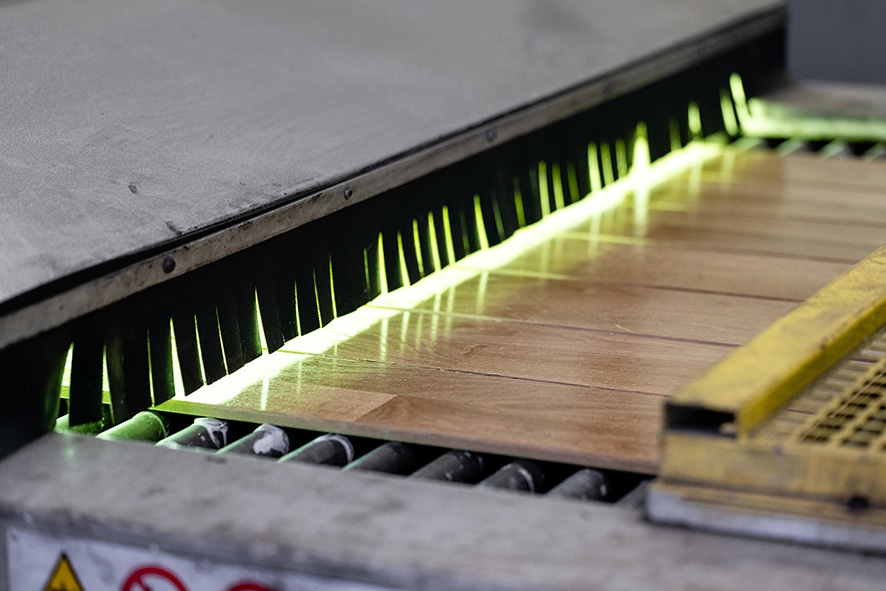
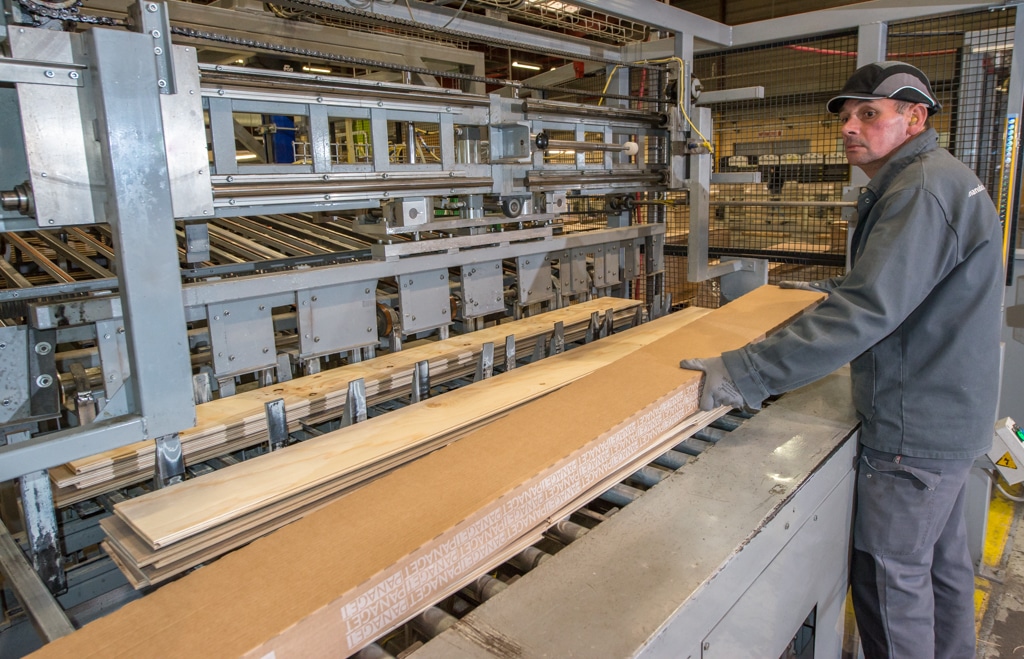
Oil or Lacquer Finish
At this stage, the wood floor is given its final appearance. After the filling operation, it is sanded and brushed to give it the desired texture. Applying an oil or lacquer finish defines the colour and the matt or satin look of the wood floor. This is complemented by several intermediate coats, known as “sealers,” which create the finish’s durability. The finishes are formulated in compliance with REACH regulations. Production batches are checked every 30 minutes to ensure colours consitancy.
Packaging
Finally, the wood floor is ready for packing to protect it during transport and storage. We use microporous film to prevent condensation, which could affect the wood floor’s stability, while ensuring the package remains sealed.
Find our wood floors and wall panelling at Panaget brand ambassador retailers in France and in over 30 countries worldwide.